Seven Ways ServiceNow Drives Digital Transformation in Manufacturing
With year-end revenue listed at $8.97 billion and an enterprise value of over $143 billion to close out 2023, ServiceNow is clearly set to continue automating IT management workflows as a large cloud-based, cross-industry platform. By smoothly integrating with third-party tools, apps, and plugins, the company facilitates the management of projects, teams, and customer interactions.
Being an official partner of ServiceNow, with deep knowledge in platform implementation, automation, customization, integration, and support, Infopulse has prepared detailed research on how this solution helps manufacturing businesses accelerate digital transformation by responding to the most complicated industry-specific challenges.
ServiceNow for Manufacturing: Key Business Use Cases
Manufacturers continue investing in a smart factory approach, thus aiming to solve ever-evolving challenges like an uncertain global economy, customer centricity, skills gap, labor shortages, and competition. According to a study by Deloitte, a stunning 86% of manufacturing executives think innovative, smart factory solutions will be the key drivers of competitiveness over the next five years. Here is where the ServiceNow platform, with its smart capabilities, steps in to accelerate factory digitization in a number of ways.
Operational Technology Management
Industry 4.0 greatly influenced manufacturing, making technologies and operations interconnected and complex. Given the fact that 74% of manufacturers still rely on legacy software and manual workflows, there is need for a context-based view of their Operational Technology (OT) environment. In this respect, ServiceNow is able to digitize operational and production processes.
- Visibility Module identifies OT assets, dependencies, and relationships, as well as maps asset criticality to get contextual insights for better OT management.
- OT Vulnerability Response monitors all existing in-house systems and partner ecosystems to discover asset vulnerabilities and swiftly notify the responsible person.
- OT Service Management uses built-in ML and contextual help to quickly address incidents and recover from them through bottleneck elimination and intelligent change management.
Such smart mechanisms help manufacturers to get an array of benefits. This includes minimized risks thanks to enhanced response and recovery, slashed maintenance costs through the reduction of redundant resources, increased security and plant safety, and boosted productivity due to process digitalization.
Supply Chain Management
Supply chain disruptions are not new; in fact, their worldwide number continues growing, with 8,197 cases happening during the first half of 2023 alone. In manufacturing, supply chain disruptions cause significant delays in product shipment and other key operations, which result in decreased productivity, revenue loss, and customer dissatisfaction.
To avoid negative consequences, manufacturers rely on the ServiceNow platform as a centralized solution for orchestrating and automating mission-critical processes, including:
- Sourcing and Procurement Operations (SPOs). ServiceNow enhances SPOs with advanced search capabilities and chat tools, a knowledge base that has a virtual assistant, and smart workload and SLA-driven intelligence.
- Supplier Lifecycle Operations. The platform capabilities allow onboarding suppliers faster through unified playbooks, managing supplier tasks in a single workspace, collaborating effectively with an easy-to-use portal, and getting advanced supplier intelligence.
- Accounts Payable Operations. ServiceNow automates mundane tasks like non-PO invoice approvals, unifies teams and workflows on a single platform, and provides visibility into the whole process β from invoice submission to payment release.
Case in point: Infopulse helped a Swedish manufacturing company establish a scalable Self-Service Portal as a part of the ServiceNow ITSM system. The delivered solution optimized asset management, user management, license management, procurement and key supply chain management workflows. As a result, the client got faster issue resolution, real-time visibility, better flexibility, and efficiency.
By driving advanced intelligence across departments and systems, ServiceNow enables the process of identifying, analyzing, and addressing possible anomalies at any stage of the supply management process β from planning to shipment. In this way, manufacturers control the situation and minimize disruptions that are so costly for their businesses.
Workplace Safety
According to the International Labor Organization, almost 3 million people die from work-related diseases and accidents. Manufacturing is one of the most hazardous sectors, up there with professions like agriculture, forestry, and construction. Fatal injuries per year for these industries number in the hundreds of thousands. This is a huge problem, resulting in disruptions, reputation damage, and high expenses. The ServiceNow platform can minimize damage through its innovative capabilities.
- Contact tracing helps detect potentially exposed employees based on workplace data such as self-reported logs, badge scans, work shift reservations, and more.
- Intelligent incident management allows monitoring and reporting safety events, as well as analyzing root causes to take preventive or corrective measures.
- Safe Workplace Suite verifies employee health status, provides visibility into the current vaccination status, and monitors personal protective equipment in real time.
Document Management
In our technology-driven world, it is a bit surprising that digital-first document management has not yet conquered the business world. To wit, 50% of an average knowledge workerβs time is lost spent preparing documents, which results in 21% decreased productivity.
Although manufacturing does not primarily focus on document management, industry-specific processes require substantial work in this respect. Automation around file creation, processing, and management β ServiceNow can cover these and other challenges, freeing up workersβ time for more complex and tailored tasks. In particular, ServiceNow document management capabilities include the following:
- Categorization presupposes creating customized document categories to retrieve data at the click of a button, be it a batch number, weekly temperature records of production systems, or product liability information. This feature also helps find instant answers to customers, thus increasing service quality.
- Version control allows tracking changes to be made in documents with ease so that various departments can access the needed information in real time to quickly clarify queries.
- Secure sharing empowers manufacturers to share the related information with in-house specialists (across engineering, accounting, customer service, the factory floor, and other departments) and third parties such as suppliers, distributors, and regulators.
All these features around automated document management help improve collaboration and productivity, while accelerating digital transformation in manufacturing settings and getting a jump on competitors.
Order Management
A Gartner report states that about 50% of companies track their financial benefits based on customer experience (CX) indicators, and 80% expect to compete mainly based on CX. Such a focus is no surprise considering the value that happy customers bring to businesses.
In manufacturing, ensuring a high level of customer satisfaction is quite complicated. This is due to the dispersed systems used for order cycle management and, as a result, the lack of visibility into the entire process.
To address these challenges, ServiceNowβs Customer Service Management (CSM) solution comes in as a single-source-of-truth system to effectively manage orders across the full lifecycle:
- Order capture and fulfillment allows importing data from third-party systems through APIs to automatically create, decompose, and track orders, while reducing fulfillment time and meeting SLAs.
- The order tracking module delivers real-time visibility into the order status and provides post-order support. Specifically, customers can create cases on their own when they need help, which decreases customer effort and contact volume.
- Product catalog and listing functionality automates the process of creating detailed product descriptions, specifications, and attributes, as well as particular listings for product types and bundles. Price lists are also formed automatically, with different effective dates, currencies, offerings, and bundles.
By adding innovation into these key processes, manufacturers can make sure all orders are processed in a timely manner with minimal delays or hiccups.
Visits Control
Ensuring physical security is as important as protection from cyber attacks. In recent years, the worldwide physical security market has grown significantly, reaching revenue numbers of $143.5 billion in 2023. The manufacturing sector contributed 9% to this total by investing in the protection of critical infrastructure and in-house facilities.
To prevent possible damage done by third-party agents visiting manufacturing settings, ServiceNow offers robust Visit Management capabilities. This includes:
- Promptly registering external visitors
- Specifying their visit dates, locations, timing, parking, and Wi-Fi requirements
- Adding customized notes for VIP guests
Admins have a transparent view over all the current and expected visits, printing access badges and updating guest status during the day. The system simplifies and secures registration for off-site workers too, notifying them with all the information they need during their visit.
Building access security is also fortified through advanced badge management functionality. By continuously monitoring badge reader information, the system can detect suspected and potentially exposed users and automatically deactivate badges. Such measures do not only eliminate security gaps, but also ensure the continuous compliance with proactive policy enforcement.
Vendor Management
Another use case worth mentioning is managing vendor services. ServiceNow presents a great platform for performing this task in an automated and effective way. Manufacturers get a single-pane view of all the vendor relationships, which helps them make more data-driven decisions and increase overall efficiency.
The featured parameters include:
- Comprehensive vendor information, including contacts, service details, and investments
- Vendor satisfaction scores based on surveys from stakeholders and subscribers
- Success indicators to analyze vendor work against KPIs, not vendor self-reporting
- Compliance monitoring to prevent service issues and ensure good governance
- Automatic calculation of service credits to enable faster refunds when vendors fail to perform according to SLAs or other contractual obligations
Automation around all these aspects will help track vendor work in a more meaningful way, control costs by targeting duplicate services across vendors, and enhance end-user experiences.
Benefits from ServiceNow Implementation
The incorporation of ServiceNowβs cutting-edge features and modules will give you a significant step up in managing your key manufacturing processes. Hereβs how:
- Improved decision-making. The platform offers robust data management capabilities, making data accessible for advanced analytics and reporting. You can quickly make informed strategic decisions with value-rich insights into:
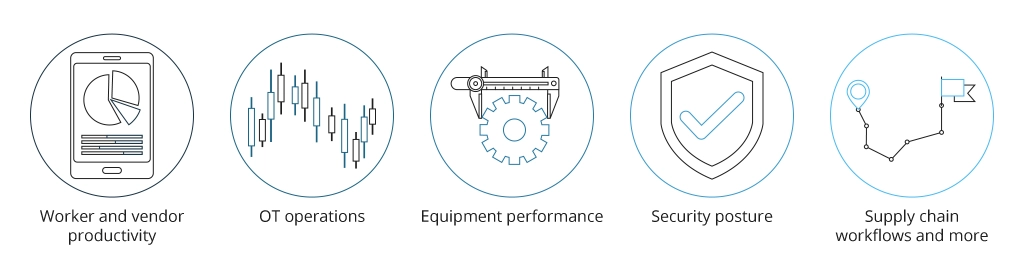
- Repetitive task automation. Account payable operations, SPO workflows, document management, visits control β these and other processes can be fully automated. In this way, managers have more time to spend on performing skill-required tasks, and overall productivity is increased.
- Risk mitigation. With advanced intelligence across the entire supply chain management lifecycle, manufacturers can detect and rapidly address anomalies, preventing service disruption. Furthermore, innovation around visit and badge management levels up improving physical security in manufacturing settings.
Itβs Time to Act
When implemented correctly and securely, the ServiceNow platform is able to revamp manufacturing processes, bringing stakeholders more tangible value. If you have already set your mind to introducing this solution to your business, team up with an experienced ServiceNow partner like Infopulse. We have the specific knowledge and skills to make the implementation process go off without a hitch. Our service offering includes:
- Comprehensive consulting on ServiceNow architecture and implementation
- Integration of ServiceNow Products
- Full-fledged migration to ServiceNow
- Innovation around platform automation and orchestration
- Seamless, secure integrations with business applications and cloud services
- ServiceNow maintenance and support
- Platform customization and tailored app development